Industrial Equipment
The Complete Guide to Saw Blades: Benefits of Each Type
The saw blade is the spinning disc on a circular saw that cuts through the material. The size of a saw blade is determined by its diameter. Circular saws are available in a variety of sizes and there are blades to match. Saw blades for cutting wood tend to be larger than those for cutting metal, for example, because wood is thicker than steel. In general, the larger the blade diameter, the more powerful the motor. The number of teeth on a blade helps determine both its function and the speed at which it cuts. Blades with more teeth cut faster, but they don’t have as aggressive action as blades with fewer teeth. A carbide-tipped blade is harder and lasts longer than one made entirely from steel.
Blade Types
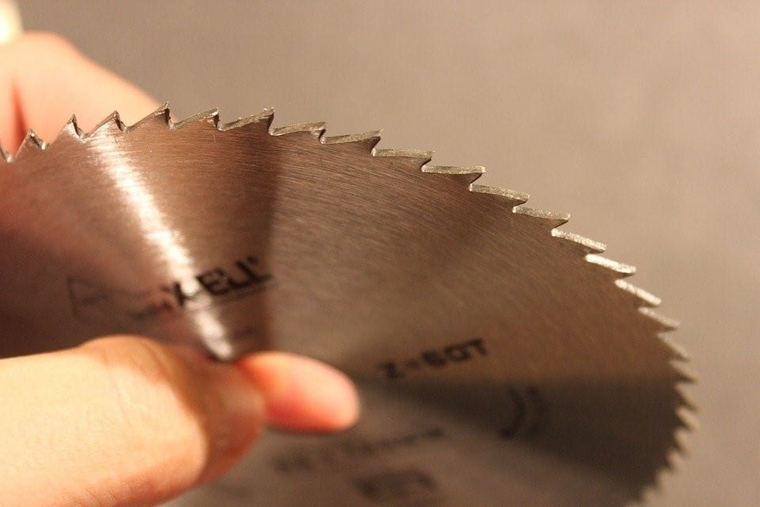
Woodworking blades have teeth designed to cut wood cleanly and smoothly, helping to minimise splintering on the top surface of a piece of wood and chipping on the bottom edge. Cutting-edge teeth typically alternate between a small triangle shape and a large trapezoid shape (called rakers). This combination helps clear sawdust from the cut area so that it doesn’t get stuck under the blade, causing kickback or burning. There are three basic types of tooth patterns:
- Crosscut: Crosscutting blades have teeth ground with alternating top bevel (ATB) angles. They perform two functions simultaneously, crosscutting wood along its grain as well as ripping it. The angle of each tooth can be anywhere between 10° and 25°. Generally, the more frequently a blade is used for crosscutting, the lower the tooth angle should be. A higher ATB angle is better for ripping because the teeth cut faster through fibre in the direction of its growth. ATB teeth are usually honed to an included angle of 40°-60°. Blades with fewer teeth have higher angles than those with more teeth to help them remove waste material quickly when cutting across the grain.
- Rip: Rip blades have teeth designed to cut with the grain of the wood. Rip blades are optimised for straight cuts along the length of a board or panel. If a blade is only used for rip cutting, it should be labelled as such. However, most all-purpose and combination blades can be used for rip cutting.
- Combo: Combo blades can be used for rip or crosscutting, but are not optimised for either. Combo blades save money by combining two types of tooth patterns into one blade, but don’t perform as well as specialised rip or crosscut blades.
Other Types of Blades
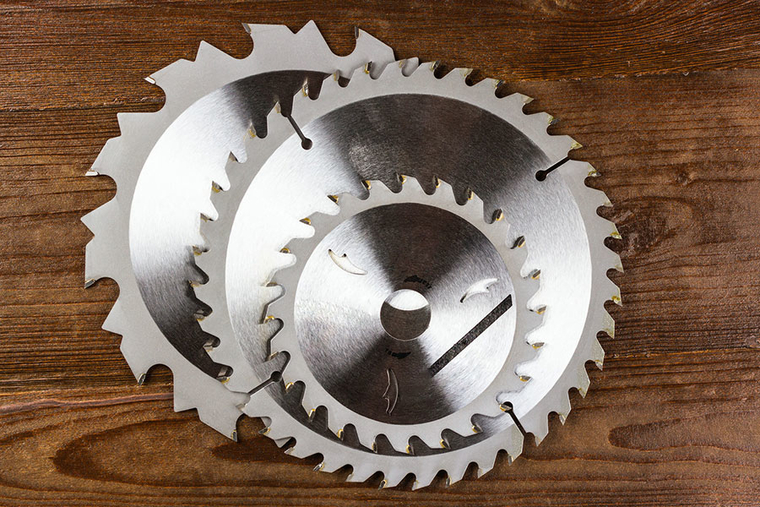
The most common type of hand-held circular saw blade has a round hole in the centre. The hole is sized to fit on the arbour that holds it in place on the saw. This type of blade is commonly referred to as full-kerf. Bulky blade teeth cut through the material easily, but the excess metal makes for a heavier blade and more resistance when cutting. The extra weight can strain the saw motor and slow down the cutting speed.
Thinner-kerf blades have a smaller diameter than full-kerf blades, so they weigh less and require less power to cut through materials. For example, a 10-inch thin-kerf blade may only have an 8 1/2 inch diameter, while a full-kerf blade could have a 9 1/2 inch diameter.
For some tasks, such as cutting metal or masonry, speciality blades are available with carbide tips and other features that maximise cutting speed and durability. The types used in a sawmill determine the quality and appearance of lumber. A sawmill operator must understand how saw blades work and how to select the best blade for each job. Several factors affect the performance of a saw blade. Some are obvious, some not.
Blade Pitch
The pitch describes the thickness of the blade, measured in thousandths of an inch. For example, a 1-inch blade with a pitch of 025 has a thickness of 025 thousandths or 25 hundredths (0.025) of an inch. This dimension is important because it impacts the amount of “set” on the teeth, which determines how well they bite into the wood and how smoothly they cut it.
A wide blade has more sets than a narrow blade, so it produces smoother cuts in softwoods that are not dense or knotty. However, wide blades tend to bend when cutting hardwoods and need more horsepower to drive them through wood than narrow blades do.
Different manufacturers use different measurements to determine the pitch of their blades. For example, one manufacturer may measure from point to point between two adjacent teeth, while others measure from gullet to gullet between two adjacent sets of teeth on opposite sides of the blade. Look for direct comparisons from one manufacturer to another whenever possible. A 10-point blade is not necessarily thicker than an 8-point blade; it depends on how manufacturers make their measurements.
Ground Clearance
Not to be confused with the set, this refers to the underside of each tooth, which needs to be angled or ground properly so that it doesn’t rub against wood fibres as it cuts. This is especially important on crosscut blades used for panelling or dimension lumber, where the material is usually 2 inches thick or less, but it’s also important on rip blades because they cut more slowly than crosscut blades and therefore have more contact with the workpiece.
Writing for the blog since 2012, Chris simply loves the idea of providing people with useful info on business, technology, vehicles, industry, sports and travel – all subjects of his interest. Even though he sounds like quite the butch, he’d watch a chick flick occasionally if it makes the wife happy, and he’s a fan of skincare routines though you’d never have him admit that unless you compliment his impeccable skin complexion.
