Automotive
The Art and Science of Custom Aluminium Castings in Automotive Performance
From low-restriction air filters to even lower-restriction exhausts, there’s a core of aftermarket parts that automotive tuners and high-performance enthusiasts reflexively turn to in search of power. These are proven, off-the-shelf parts that can give any car a respectable, Australian Design Rule (ADR) compliant bump in output without breaking anyone’s budget. Some enthusiasts, however, want more than off-the-shelf performance; that means they need tuning specialists with the knowledge and capacity to actually build high-performance parts, not just package them.
It takes more than just good intentions to excel at engineering and manufacturing one-off car parts, though; and while there’s no shortage of engineering expertise in Australia, it takes a company that understands regulatory, as well as technical requirements to turn a power-producing concept into a function component. That’s the benefit a custom parts engineer like Adelaide’s Harrop Casting Technologies (CT) brings to the table.
Take Performance to the Edge with Custom Aluminium Castings
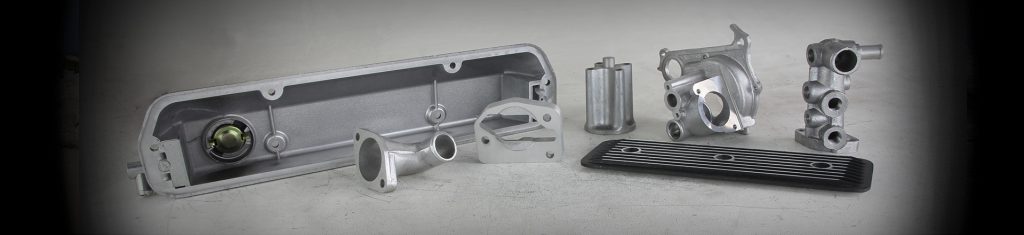
Ask any experienced engine tuner and they’ll tell you that real high performance isn’t bolted on, it’s built on. It takes engineering know-how to build high performance though, and Harrop CT is the specialized aftermarket car parts producer that enthusiasts trust to build performance. They know that even the most unlikely parts can make a difference; and from one-of-a-kind non-ferrous aluminium parts castings, to custom fabrications in brass, magnesium, and other alloys, they have the skill to help enthusiasts realise the incremental power increases that can add up to big, reliable power gains.
It’s no secret that aluminium is the preferred favourite alloy when it comes to either high-performance OE, or off-the-shelf auto parts. However, when serious performance enthusiasts have the latitude to pursue prototype aftermarket auto parts, custom aluminium castings let them take performance to the edge with a core of benefits that include:
- A significant weight reduction over OE steel or iron parts, but with no loss of strength;
- The ability to refine or redesign OE components for improved heat dissipation; and,
- A unique appearance that allows you to accommodate other modifications.
If you want high-performance auto parts that are capable of delivering extraordinary results while offering a custom aesthetic, aluminium parts castings are perfect for late-model cars that have already received some aftermarket tuning, as well as vintage custom rides and hot rods. Most importantly though, depending on the application, companies like Harrop CT can ensure that any custom castings they manufacture are in full compliance with all relevant ADR requirements, are less prone to fatigue or failure than their forged or billet equivalents, and are mechanically and thermally compatible with your higher output requirements.
Custom Castings Give You the Street and Competition Advantage
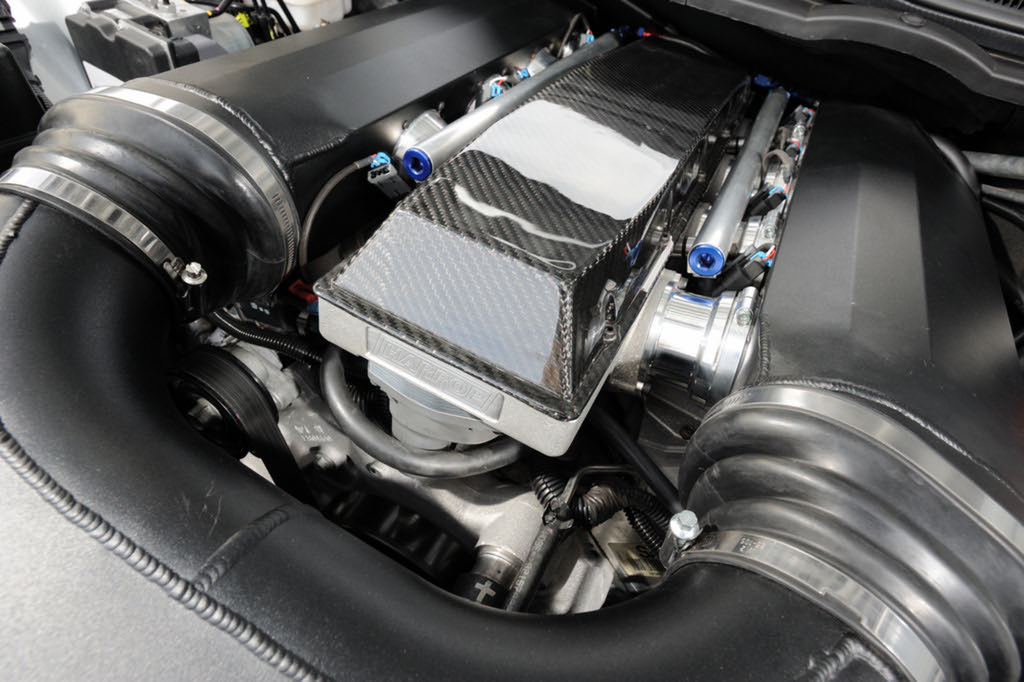
Make no mistake: the sheer range of high-performance parts that can be custom cast from lightweight aluminium alloy is virtually unlimited. Any standard, or high-performance auto part that’s forged or pressed from stee; or iron can be successfully recast in 319, 356 / A356, or 535 alloys, heat treated to T5, T6, or T7 standards, and shot-peened for final hardening.
ISO 9001:2015 certified aftermarket car part manufacturers like Harrop CT can produce a full assortment of special and prototype castings for all kinds of daily and limited use, including:
- Redrilled aluminium bell housings, shift forks, and bottom-end support;
- Custom intake manifolds, water inlets, and injection runners;
- Custom transmission pans, oil pans, and oil reservoir tanks;
- Specialized alloy valve covers and engine brackets; and,
- Custom intercooler, air filter, and ram air boxes and ducts.
Even modest reductions in weight and heat transfer can translate to increases in output and acceleration; and in the absence of reworking, any combination of these lightweight car performance part castings is going to see a performance advantage. When it comes to performance parts for competition vehicles, Harrop CT can go the full length with the design, engineering, inspection, and testing of racing-body sanctioned powerplants and components, including:
- Custom engine blocks and gearboxes;
- Cylinder heads and engine internals; and,
- Custom cast turbochargers and superchargers.
Ideally, no matter if you’re looking for moderate, ADR-compliant gains that can be expected with shedding unnecessary kilos, or a custom intake that’ll give your sprintcar racer a double-digit jump in output, you can be sure that an aftermarket auto part manufacturer like Harrop CT has the know-how to produce the car performance parts you need.
Common Casting Technologies that Produce Exceptional Results
Technology is everything when it comes to high-quality aftermarket performance car parts castings, and as their name suggests, technology is the cornerstone of everything that Harrop CT does. It’s most crucially reflected in their casting processes though, where they rely on the 3 most common casting methods to perform their manufacturing: Gravity Die Casting, Sand Casting, and Core Blowing.
- Large volume Gravity Die Casting. Gravity die casting involves the pouring of molten aluminium into steel moulds, and is used for complex, and large-volume aftermarket parts runs.
- Composite Sand Casting. Sand casting involves the filling of „green“ sand moulds bonded together by composites, and is used primarily for low-volume part runs.
- Resin covered Core Blowing. Core blowing uses resin-covered sand with disposable moulds, and offers improved accuracy and higher productivity rates than composite sand casting.
Regardless of the type of casting method used for your parts, you can be sure that Harrop CT can perform all the secondary processing, testing, and even material finishing to make sure that the final product exceeds all your performance and reliability expectations.
The Final Word
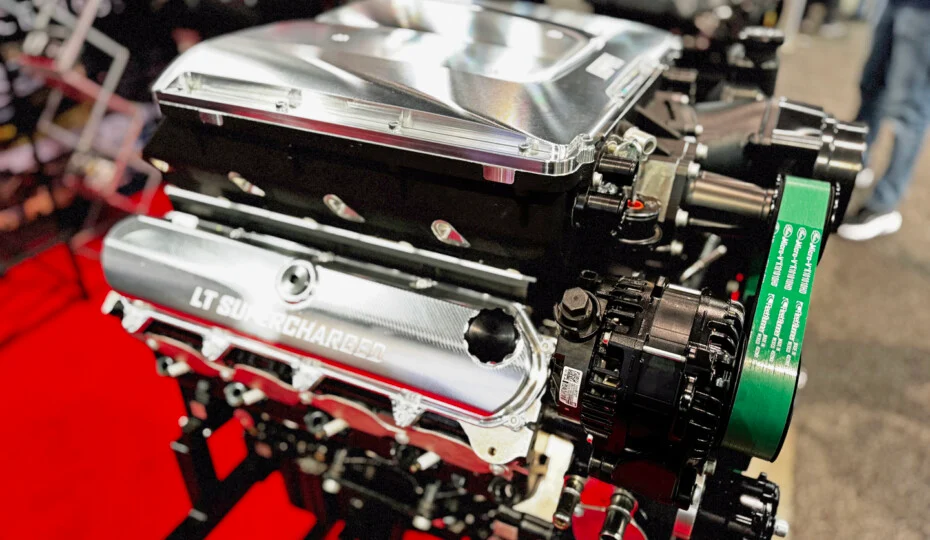
At the end of the day, while there’s no shortage of aftermarket parts available for performance enthusiasts to bolt on, serious enthusiasts can’t ignore the power gains that can be achieved by building in performance. It takes the assistance of specialists with the knowledge, technical expertise, and capacity to isolate that potential properly though, and to do it in a manner that’s ADR-compliant.
Adelaide’s Harrop CT specializes in unleashing the built-in performance in aftermarket car parts and engine castings. They know where your engine’s sustainable performance is locked in, and they know how to bring it out.
Writing for the blog since 2012, Chris simply loves the idea of providing people with useful info on business, technology, vehicles, industry, sports and travel – all subjects of his interest. Even though he sounds like quite the butch, he’d watch a chick flick occasionally if it makes the wife happy, and he’s a fan of skincare routines though you’d never have him admit that unless you compliment his impeccable skin complexion.
